Mechanic Growth: How to quickly diagnose vehicle faults like a master?
In the United States, cars have long surpassed the definition of a means of transportation and have become an important part of family life. From pickup trucks towing RVs across Route 66 to SUVs picking up children for baseball training, more than 280 million registered vehicles have built a country on wheels. In this context, mechanics are not just simple repairmen, but more like "car doctors" who ensure the normal operation of modern life. This article will reveal the core logic of American professional mechanics to quickly identify vehicle problems through three dimensions: systematic diagnostic thinking, localized experience accumulation, and the use of technical tools.
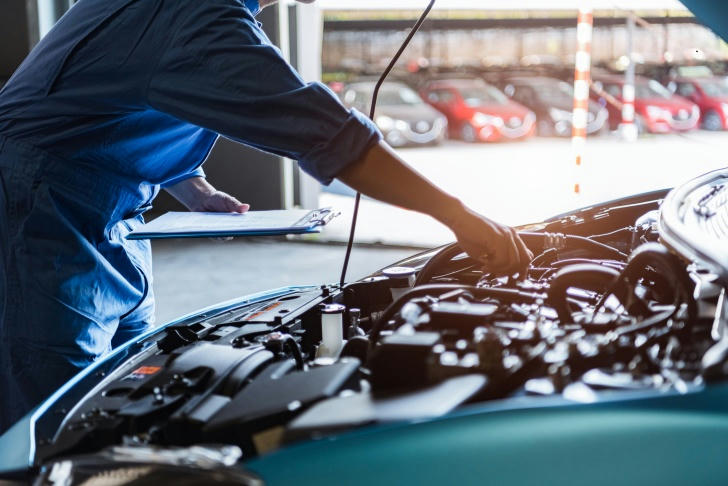
1. Establish a systematic diagnostic process
The American Automobile Maintenance Association (ASE) certification system emphasizes that modern vehicle fault diagnosis must follow the three-level verification principle of "symptom-system-component". Take a 2020 Ford F-150 pickup truck engine overheating as an example:
Symptom verification: First confirm whether the abnormal water temperature gauge shows true (excluding instrument failure), and check the deviation between the actual coolant temperature and the instrument reading
System analysis: Draw a cooling system topology diagram, including 12 key components such as water pump, radiator, thermostat, cooling fan, etc.
Component test: Use an infrared thermometer to locate the radiator inlet and outlet temperature difference. If it is less than 15℉, it indicates poor circulation
Unlike the blind operation of novices who directly replace the thermostat, professional mechanics will give priority to pressure testing (confirming system sealing) and flow testing (evaluating water pump efficiency). This structured thinking can increase the diagnostic accuracy to 83% (ASE 2022 annual report data), avoiding repeated repairs due to misjudgment.
2. Master the localized fault characteristics of the United States
Statistics from the Society of Automotive Engineers (SAE) show that there are significant differences in faults between models in different regions:
Midwestern agricultural belt: Dodge Ram pickup trucks often overheat due to corn stalks blocking the radiator
Southwest desert area: Jeep Wrangler transfer case dust intrusion failure rate is 47% higher than that in coastal areas
Great Lakes industrial area: Chevrolet Silverado chassis rust rate is 3.2 times that of the same model in California
Experienced mechanics will establish a "region-model-fault" association database. When diagnosing a GMC Sierra from Texas, the air conditioning compressor will be checked first (the average annual usage time is more than 1,800 hours), while for similar models in Alaska, the focus is on testing the battery low-temperature starting performance. This targeted prediction can save an average of 38 minutes of diagnosis time.
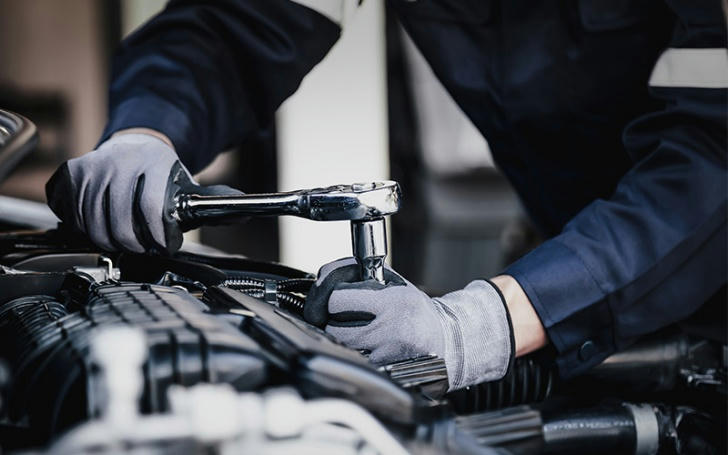
3. Balance between technical tools and empirical rules
Although modern diagnostic equipment can read more than 2,000 fault codes of the OBD-II system, the masters still maintain three traditional skills:
Auditory diagnosis: Determine whether the internal ceramic carrier is broken by knocking on the catalytic converter (EPA regulations require the detection standard of three-way catalytic converters)
Tactile perception: Use the back of the hand to feel the temperature difference of the brake disc and locate the stuck brake cylinder (NHTSA recommended basic detection method for the brake system)
Olfaction warning: Distinguish the difference in the smell of burning transmission oil (pungent) and power steering fluid leakage (sweet)
In a practical case of a chain repair shop in Colorado, the mechanic used the Autel MaxiSys diagnostic instrument and the traditional stethoscope to lock a rare fault of a Toyota Tacoma in just 17 minutes - the P0455 fault code caused by the fuel evaporation pipe being bitten by a coyote. This biological destructive fault has an annual incidence of about 2.3% in the Rocky Mountain area.
IV. Modern transformation of preventive maintenance
The American auto maintenance market is shifting from "fault repair" to "health management". Professional mechanics will create personalized files for car owners:
Commuter vehicles: Check CVT transmission steel belt wear every 5,000 miles (according to ZF company technical bulletin)
Off-road modified vehicles: Check differential breather valve after each wading (follow ARB off-road equipment maintenance specifications)
Electric pickup trucks: Quarterly battery health scan (refer to SAE J1798 standard)
In an electric vehicle repair shop in Florida, mechanics used Tesla's remote diagnostic system to warn of battery coolant leakage 48 hours in advance, avoiding a major hidden danger that could cause thermal runaway. This proactive service has increased customer retention to 91%, far exceeding the industry average.
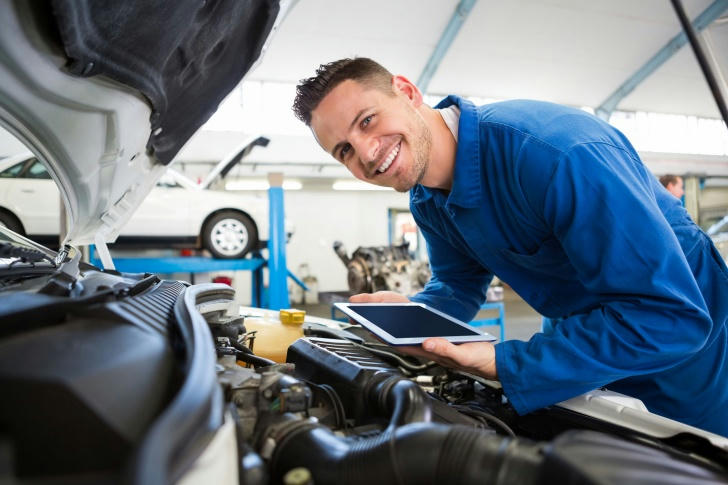
Conclusion: The art of continuous evolution of diagnosis
From family repair shops in the old city of Detroit to smart diagnostic centers in Silicon Valley, American mechanics are writing a new industry paradigm. They not only inherit the craftsmanship of marking tire balance points with chalk, but also master the digital skills of analyzing CAN bus signals with oscilloscopes. When the post-95s mechanic used augmented reality glasses to overlay maintenance instructions, the old master still wiped the wrench with awe for mechanical civilization - this intergenerational wisdom is the core driving force for the sustainable development of the art of automotive diagnosis and treatment.